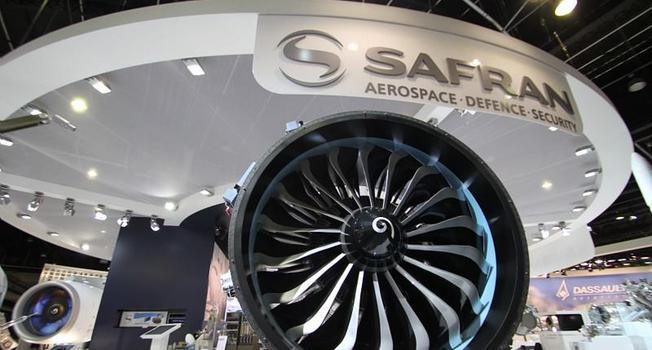
Added substance fabricating, otherwise called 3D imprinting in different commercial ventures, utilizes PC supported outline, building, assembling and materials science programming (CAD/CAE/CAM/CAMS) to make 3D models of parts and subsystems that are then manufactured utilizing progressive layers of materials. The viable utilization of this assembling process in the flight business can improve creation times and in addition item execution regarding quality, weight and natural effect upgrades that are difficult to get with customary routines.
The association joins Dassault Systèmes' 3DEXPERIENCE stage with Safran's mastery in inventive innovations, for the improvement of a world-class, end-to-end computerized answer for added substance fabricating. This new end-to-end procedure will address upstream material outline and downstream assembling procedures and testing to give advanced progression to every designing parameter important for the added substance assembling of a motor part: material science, useful detail, generative configuration, 3D printing enhancement, multi-mechanical creation and affirmation.
"Dassault Systèmes' long history of joint effort with Safran is presently tackling another measurement to grasp and incorporate new materials and techniques for building, creation and support that will fundamentally affect the aeronautics business," said Dominique Florack, Senior Executive Vice President, Research & Development, Dassault Systèmes. "Our 3DEXPERIENCE stage's technique covers all parts of the added substance assembling procedure, from material configuration to reasonable outline, generative configuration to assembling, and accreditation to repair. Together with Safran, we can sustain virtual world procedures for a complete approach in this field that will help reform tomorrow's assembling."
"Examination and innovation is a major piece of Safran, permitting us to drive constant upgrades for more secure and more ecological amicable air travel," said Pierre Fabre, Senior Executive Vice President R&T, Innovation, Safran. "Safran is right now driving the field in utilizing 3D printing innovation to make its motors.
Reference:
http://www.businesswire.com/news/home/20150617006278/en#.VYJU__mqqko
The association joins Dassault Systèmes' 3DEXPERIENCE stage with Safran's mastery in inventive innovations, for the improvement of a world-class, end-to-end computerized answer for added substance fabricating. This new end-to-end procedure will address upstream material outline and downstream assembling procedures and testing to give advanced progression to every designing parameter important for the added substance assembling of a motor part: material science, useful detail, generative configuration, 3D printing enhancement, multi-mechanical creation and affirmation.
"Dassault Systèmes' long history of joint effort with Safran is presently tackling another measurement to grasp and incorporate new materials and techniques for building, creation and support that will fundamentally affect the aeronautics business," said Dominique Florack, Senior Executive Vice President, Research & Development, Dassault Systèmes. "Our 3DEXPERIENCE stage's technique covers all parts of the added substance assembling procedure, from material configuration to reasonable outline, generative configuration to assembling, and accreditation to repair. Together with Safran, we can sustain virtual world procedures for a complete approach in this field that will help reform tomorrow's assembling."
"Examination and innovation is a major piece of Safran, permitting us to drive constant upgrades for more secure and more ecological amicable air travel," said Pierre Fabre, Senior Executive Vice President R&T, Innovation, Safran. "Safran is right now driving the field in utilizing 3D printing innovation to make its motors.
Reference:
http://www.businesswire.com/news/home/20150617006278/en#.VYJU__mqqko