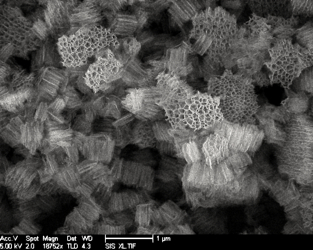
Researchers at UCLA indicate the potential for magnesium to be for the 21st century what aluminum was for the 20th century.
In a new paper that was published recently, researchers have said that one idea for improving the structural stability of soft metals like magnesium as proposed by materials scientists has been to disperse silicon carbide nanoparticles in a molten metal.
A lot more structural strength to metals would then be provided by the nano particles when the metal is cooled, making them more useful for certain applications.
Despite being one of the most abundant metals in the Earth’s crust, aluminum was one of the most expensive metals on Earth in the mid-19th century. The expensive and complicated process was the reason for this as the process needed to turn it from its natural state to the metal we all enjoy.
With the development of the Hall–Héroult process in the late 1880s this aspect of aluminum manufacturing changed. The Hall–Héroult process enabled aluminum to be cheaply manufactured and led to its widespread use in everything today from building frames to soda cans to airplanes.
Magnesium is made easy and cheap to manufacture as a side effect of the Hall-Héroult process. As magnesium is even lighter than aluminum and is also very abundant in the Earth’s crust, this has some potential manufacturing benefits. It can be used in many similar applications – opening the door for more energy efficiency and other benefits.
However the softness of magnesium make it ideal for composing alloys of aluminum and other metals. However the same structural applications we use aluminum in makes the alloys composed primarily of magnesium less useful.
The new paper by the UCLA researchers says that the challenge in making magnesium harder is to get those nanoparticles to disperse uniformly within magnesium or other metal matrices. This is so because the nano particles have a tendency to clump together. Hence using the metal for heavy duty work like skyscrapers or airplanes is not possible without uniformity.
This is the problem that the UCLA team claims to have solved and have been able to successfully develop a process that achieved a uniform dispersion of silicon carbide nanoparticles into a molten magnesium-zinc alloy.
A process called high-pressure torsion has been used to treat the metal. The metal was compressed while undergoing torsional strain during this procedure. This process has been used to produce highly homogeneous metal with great strength in recent decades.
An alloy that has 86% magnesium alloy and 14% silicon carbide is the result of the process, according to the researchers. This result has some promising properties for applications.
“An enhancement of strength, stiffness, plasticity and high-temperature stability is simultaneously achieved, delivering a higher specific yield strength and higher specific modulus than almost all structural metals,” the researchers wrote in their paper.
“It’s been proposed that nanoparticles could really enhance the strength of metals without damaging their plasticity, especially light metals like magnesium, but no groups have been able to disperse ceramic nanoparticles in molten metals until now,” said Xiaochun Li, principal investigator on the research, said in a press release.
(Source:www.forbes.com)
In a new paper that was published recently, researchers have said that one idea for improving the structural stability of soft metals like magnesium as proposed by materials scientists has been to disperse silicon carbide nanoparticles in a molten metal.
A lot more structural strength to metals would then be provided by the nano particles when the metal is cooled, making them more useful for certain applications.
Despite being one of the most abundant metals in the Earth’s crust, aluminum was one of the most expensive metals on Earth in the mid-19th century. The expensive and complicated process was the reason for this as the process needed to turn it from its natural state to the metal we all enjoy.
With the development of the Hall–Héroult process in the late 1880s this aspect of aluminum manufacturing changed. The Hall–Héroult process enabled aluminum to be cheaply manufactured and led to its widespread use in everything today from building frames to soda cans to airplanes.
Magnesium is made easy and cheap to manufacture as a side effect of the Hall-Héroult process. As magnesium is even lighter than aluminum and is also very abundant in the Earth’s crust, this has some potential manufacturing benefits. It can be used in many similar applications – opening the door for more energy efficiency and other benefits.
However the softness of magnesium make it ideal for composing alloys of aluminum and other metals. However the same structural applications we use aluminum in makes the alloys composed primarily of magnesium less useful.
The new paper by the UCLA researchers says that the challenge in making magnesium harder is to get those nanoparticles to disperse uniformly within magnesium or other metal matrices. This is so because the nano particles have a tendency to clump together. Hence using the metal for heavy duty work like skyscrapers or airplanes is not possible without uniformity.
This is the problem that the UCLA team claims to have solved and have been able to successfully develop a process that achieved a uniform dispersion of silicon carbide nanoparticles into a molten magnesium-zinc alloy.
A process called high-pressure torsion has been used to treat the metal. The metal was compressed while undergoing torsional strain during this procedure. This process has been used to produce highly homogeneous metal with great strength in recent decades.
An alloy that has 86% magnesium alloy and 14% silicon carbide is the result of the process, according to the researchers. This result has some promising properties for applications.
“An enhancement of strength, stiffness, plasticity and high-temperature stability is simultaneously achieved, delivering a higher specific yield strength and higher specific modulus than almost all structural metals,” the researchers wrote in their paper.
“It’s been proposed that nanoparticles could really enhance the strength of metals without damaging their plasticity, especially light metals like magnesium, but no groups have been able to disperse ceramic nanoparticles in molten metals until now,” said Xiaochun Li, principal investigator on the research, said in a press release.
(Source:www.forbes.com)