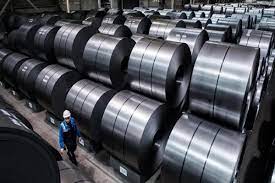
Steel tycoon James Brand speaks above the sound of metal being poured into a foundry furnace, explaining how rising expenses have forced him to hike his rates by 70 per cent.
Despite the significant price increase, he claims that his customers in industries such as oil and gas, automobiles, and construction are placing new orders at an all-time high. His backlog of orders has grown from 4-6 weeks to 6 months.
Clients expect more price increases at a time when the cost of pig iron and scrap metal is skyrocketing due to the Ukraine conflict, and the massive amount of energy required to melt the two inputs into cast iron has never been higher.
"With raw materials and costs escalating, customers are thinking, 'If I don't buy now, in two months it will be even more expensive,'" Brand said amid the heat, dust and hubbub of United Cast Bar's (UCB) factory in a part of northern England that once powered the Industrial Revolution.
"People are placing orders ahead, to try and fix as many costs as they can."
UCB, which previously struggled to raise prices at all, is now doing so on a monthly basis and steadily marking them up, incurring additional costs that will permeate into global manufacturing lines, fueling inflation and a consumer cost-of-living issue.
Despite the price increases, Brand said the business was still under pressure. He stated UCB's gross margin had declined by around 6%, without providing specific details.
Steelmakers and other industrial enterprises across Europe are experiencing similar issues. They're the result of skyrocketing power prices due to a supply shortage, as well as the ongoing COVID disruption and Russia's invasion of Ukraine, both of which are key pig iron producers.
However, the situation is particularly dire in the United Kingdom. Due to environmental policies, a reliance on gas, and higher power transmission and carbon permit costs than in Europe, the steel sector there faces electricity rates that are 50-60% higher than in Germany and France.
This is problematic for companies like UCB, which uses a lot of electricity to run its two 8-tonne electric-induction furnaces, which reach temperatures of over 1,400 degrees Celsius to melt scrap and pig iron before being poured into a receiver to be cast into the desired shape and cooled before being shipped to Europe, the Americas, Australia, New Zealand, or within the United Kingdom.
This procedure consumes 24 gigawatt hours of energy and up to 22 gigawatt hours of gas per year, making the company one of the country's most demanding power users.
UCB's energy bill would normally be roughly 250,000 pounds ($326,000) every month, according to Brand. It reached 450,000 pounds in March.
"It's a hefty bill," added Brand, the fourth generation of his family to work in the metals and steel industry, from the site in Chesterfield, a town in the orbit of the northern English city of Sheffield, historically famed for its steel.
"It's even worse at the moment."
The magnitude of the electricity price increases facing Britain's manufacturers, who account for approximately a tenth of the country's economic activity, is being exacerbated by rising raw material costs.
In the year to March, such costs increased by more than 19 per cent, the highest yearly increase since records began in 1997 and considerably above the long-term average of roughly 2 per cent.
Steve Elliott, the head of the Chemical Industries Association in the United Kingdom, a trade group for another energy-intensive industry, said his companies had to tightly control power and gas usage.
Chemical, glass, and steel companies, for example, have been able to cope as a fundamental sector that provides items needed by so many other sectors, as long as they can pass price increases on to customers, he says.
"It's just that businesses are becoming less able to do that. As each month passes, demand softens as the cost of living increasingly bites."
Brand agreed, stating that his pig iron bill increased from around 400 euros ($435) per tonne in 2020 to 650 euros by the end of 2021. He's now valued at 1,000 euros or more.
He is concerned that his prices will eventually reach a point where clients would be unable to afford them, resulting in a drop in demand and, in the rollercoaster ride that a pandemic and war have produced for businesses, a new downward cycle.
When asked if he can operate in the current environment, Brand answers he can as long as clients accept the price rises.
"It gets tight and margins get slimmed out (but) we're still surviving," he said.
Indeed, authorities are keeping a careful eye on UK companies' capacity to pass on their rising costs to customers as they try to determine how long the recent surge in consumer price inflation will last.
The global economy has been suffocated by a lack of employees, cargo ships, and resources, driving price increases in everything from food and furnishings to fuel and flights.
"It will be really, really crucial to see if demand slows. The Bank of England is very focused on that," Morgan Stanley economist Bruna Skarica said.
"For the BoE to feel comfortable that inflation will fall back to 2%, they do need to see pricing power come off and that will happen when demand slows."
Across Europe, rising energy costs have caused energy-intensive enterprises to limit or cease operations, often hour by hour, depending on the current cost of electricity.
Even ArcelorMittal, the world's largest steelmaker, has been running its electric arc furnaces in various European locations in a stop-start mode for months to avoid paying peak electricity prices, which would be devastating to its bottom line.
Due to dwindling demand from the auto industry, Thyssenkrupp has reduced working hours for 1,300 of its steel workers. The auto industry, Thyssenkrupp's main client, has struggled with supply-chain disruptions and chip shortages.
Lech-Stahlwerke, a minor German steelmaker, has also halted operations at a factory in Bavaria.
"In some cases, energy prices are 10 times higher than last year," Thomas Friedrich, a member of Lech-Stahlwerke's management, told Reuters TV.
Some British steelmakers have temporarily paused output in response to rising prices, according to Frank Aaskov, policy director for energy at trade organisation UK Steel, but he declined to provide specifics.
UCB has hedged 75 per cent of its energy expenses through September, lowering its exposure to potential price swings, and had other hedges in place for the next two years, according to Brand.
The gains, however, as well as the unpredictability, are inconvenient.
The British government has admitted that the country's industrial enterprises pay greater energy expenses than their European counterparts. It said this month in a new energy strategy that it would extend a compensation programme for intensive users for another three years, a decision that industry applauded as a step toward bridging the gap in electricity pricing.
According to analysts, industry experts, and politicians, today's British manufacturers have carved out a significant position on global supply chains by supplying high-value products, and they should be able to weather the storm in the short run.
The head of Britain's parliamentary select committee on business and energy, Darren Jones, praised the recent government action but expressed concern about the long-term effects of such a severe climate.
"The scale of the energy crisis we're facing over the next year means that businesses will fail and jobs will be lost, as well as production hit, if we do not see more support," he said.
(Source:www.reuters.com)
Despite the significant price increase, he claims that his customers in industries such as oil and gas, automobiles, and construction are placing new orders at an all-time high. His backlog of orders has grown from 4-6 weeks to 6 months.
Clients expect more price increases at a time when the cost of pig iron and scrap metal is skyrocketing due to the Ukraine conflict, and the massive amount of energy required to melt the two inputs into cast iron has never been higher.
"With raw materials and costs escalating, customers are thinking, 'If I don't buy now, in two months it will be even more expensive,'" Brand said amid the heat, dust and hubbub of United Cast Bar's (UCB) factory in a part of northern England that once powered the Industrial Revolution.
"People are placing orders ahead, to try and fix as many costs as they can."
UCB, which previously struggled to raise prices at all, is now doing so on a monthly basis and steadily marking them up, incurring additional costs that will permeate into global manufacturing lines, fueling inflation and a consumer cost-of-living issue.
Despite the price increases, Brand said the business was still under pressure. He stated UCB's gross margin had declined by around 6%, without providing specific details.
Steelmakers and other industrial enterprises across Europe are experiencing similar issues. They're the result of skyrocketing power prices due to a supply shortage, as well as the ongoing COVID disruption and Russia's invasion of Ukraine, both of which are key pig iron producers.
However, the situation is particularly dire in the United Kingdom. Due to environmental policies, a reliance on gas, and higher power transmission and carbon permit costs than in Europe, the steel sector there faces electricity rates that are 50-60% higher than in Germany and France.
This is problematic for companies like UCB, which uses a lot of electricity to run its two 8-tonne electric-induction furnaces, which reach temperatures of over 1,400 degrees Celsius to melt scrap and pig iron before being poured into a receiver to be cast into the desired shape and cooled before being shipped to Europe, the Americas, Australia, New Zealand, or within the United Kingdom.
This procedure consumes 24 gigawatt hours of energy and up to 22 gigawatt hours of gas per year, making the company one of the country's most demanding power users.
UCB's energy bill would normally be roughly 250,000 pounds ($326,000) every month, according to Brand. It reached 450,000 pounds in March.
"It's a hefty bill," added Brand, the fourth generation of his family to work in the metals and steel industry, from the site in Chesterfield, a town in the orbit of the northern English city of Sheffield, historically famed for its steel.
"It's even worse at the moment."
The magnitude of the electricity price increases facing Britain's manufacturers, who account for approximately a tenth of the country's economic activity, is being exacerbated by rising raw material costs.
In the year to March, such costs increased by more than 19 per cent, the highest yearly increase since records began in 1997 and considerably above the long-term average of roughly 2 per cent.
Steve Elliott, the head of the Chemical Industries Association in the United Kingdom, a trade group for another energy-intensive industry, said his companies had to tightly control power and gas usage.
Chemical, glass, and steel companies, for example, have been able to cope as a fundamental sector that provides items needed by so many other sectors, as long as they can pass price increases on to customers, he says.
"It's just that businesses are becoming less able to do that. As each month passes, demand softens as the cost of living increasingly bites."
Brand agreed, stating that his pig iron bill increased from around 400 euros ($435) per tonne in 2020 to 650 euros by the end of 2021. He's now valued at 1,000 euros or more.
He is concerned that his prices will eventually reach a point where clients would be unable to afford them, resulting in a drop in demand and, in the rollercoaster ride that a pandemic and war have produced for businesses, a new downward cycle.
When asked if he can operate in the current environment, Brand answers he can as long as clients accept the price rises.
"It gets tight and margins get slimmed out (but) we're still surviving," he said.
Indeed, authorities are keeping a careful eye on UK companies' capacity to pass on their rising costs to customers as they try to determine how long the recent surge in consumer price inflation will last.
The global economy has been suffocated by a lack of employees, cargo ships, and resources, driving price increases in everything from food and furnishings to fuel and flights.
"It will be really, really crucial to see if demand slows. The Bank of England is very focused on that," Morgan Stanley economist Bruna Skarica said.
"For the BoE to feel comfortable that inflation will fall back to 2%, they do need to see pricing power come off and that will happen when demand slows."
Across Europe, rising energy costs have caused energy-intensive enterprises to limit or cease operations, often hour by hour, depending on the current cost of electricity.
Even ArcelorMittal, the world's largest steelmaker, has been running its electric arc furnaces in various European locations in a stop-start mode for months to avoid paying peak electricity prices, which would be devastating to its bottom line.
Due to dwindling demand from the auto industry, Thyssenkrupp has reduced working hours for 1,300 of its steel workers. The auto industry, Thyssenkrupp's main client, has struggled with supply-chain disruptions and chip shortages.
Lech-Stahlwerke, a minor German steelmaker, has also halted operations at a factory in Bavaria.
"In some cases, energy prices are 10 times higher than last year," Thomas Friedrich, a member of Lech-Stahlwerke's management, told Reuters TV.
Some British steelmakers have temporarily paused output in response to rising prices, according to Frank Aaskov, policy director for energy at trade organisation UK Steel, but he declined to provide specifics.
UCB has hedged 75 per cent of its energy expenses through September, lowering its exposure to potential price swings, and had other hedges in place for the next two years, according to Brand.
The gains, however, as well as the unpredictability, are inconvenient.
The British government has admitted that the country's industrial enterprises pay greater energy expenses than their European counterparts. It said this month in a new energy strategy that it would extend a compensation programme for intensive users for another three years, a decision that industry applauded as a step toward bridging the gap in electricity pricing.
According to analysts, industry experts, and politicians, today's British manufacturers have carved out a significant position on global supply chains by supplying high-value products, and they should be able to weather the storm in the short run.
The head of Britain's parliamentary select committee on business and energy, Darren Jones, praised the recent government action but expressed concern about the long-term effects of such a severe climate.
"The scale of the energy crisis we're facing over the next year means that businesses will fail and jobs will be lost, as well as production hit, if we do not see more support," he said.
(Source:www.reuters.com)