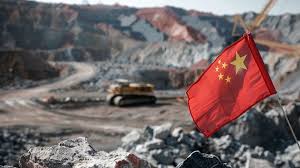
China’s shipments of rare earth permanent magnets to the United States saw a dramatic rebound in June, delivering nearly 350 metric tons to U.S. ports after months of constrained deliveries. The rebound follows Beijing’s decision to expedite export licenses that had been held up under new springtime restrictions. As American manufacturers scramble to secure these critical components for electric vehicles, wind turbines and advanced electronics, the June influx underscores China’s unrivaled influence over the rare earth magnet market—and the urgency of diversification efforts underway in the U.S.
Licensing Reforms Unleash Backlogged Shipments
In April, Chinese authorities added key magnet grades and rare earth compounds to an expanded export‑control list, triggering a licensing bottleneck that left hundreds of shipments in limbo. Exporters faced wait times of six to eight weeks for approvals, leading to missed production targets in Detroit and delayed wind‑farm installations across Texas and the Midwest. Under pressure from Beijing’s trade negotiators and frustrated U.S. industry representatives, China’s Ministry of Commerce moved swiftly in late May to streamline procedures. By early June, hundreds of pending applications were approved overnight, clearing the backlog and allowing exporters to dispatch cargoes that had accumulated over two months.
Customs data show U.S.‑bound magnet exports jumping more than 660% from May to June, a surge driven less by fresh orders than by fulfillment of existing contracts. Many shipments arrived at West Coast and Gulf Coast ports stacked high on container ships, with brokers arranging urgent trucking to battery and motor factories. Within days, assembly lines at several electric‑vehicle gigafactories had been revived, and delayed rotor components for offshore wind farms were en route to coastal staging yards. Manufacturers report that as much as 70% of the magnets delayed in spring have now reached production floors, alleviating immediate shortages but also raising questions about the reliability of future supplies.
Industry Impacts Across the Energy and Tech Sectors
Rare earth magnets—most notably neodymium‑iron‑boron (NdFeB) varieties—are the powerhouse behind high‑efficiency electric motors, wind‑turbine generators, robotics and aerospace actuators. Their exceptional magnetic strength and resistance to demagnetization make them irreplaceable in many next‑generation technologies. With domestic U.S. refining capacity still in its infancy, American manufacturers have for years depended on Chinese‑made magnets to meet rising demand.
The June surge has mitigated short‑term supply pains, allowing automakers to resume planned production increases. Several major EV producers noted that magnet shortages had risked delaying the launch of new battery‑electric models, but June’s deliveries have enabled them to keep annual output targets intact. In the wind‑energy sector, turbine OEMs report that backlog reductions now clear the way for scheduled installations of several gigawatts of new capacity before year‑end—projects that had faced months‑long delays.
Yet the reprieve is temporary. Over 90% of the world’s rare earth magnet manufacturing capacity resides in China, and roughly 60% of refined rare earth oxides likewise originate there. While U.S. policy measures—such as $2.8 billion in CHIPS and Science Act funding and a national Critical Minerals Strategy—aim to jump‑start domestic mining and separation plants, experts estimate that commercial output won’t reach meaningful scale until at least 2027. In the interim, American firms are pledging billions to build recycling programs that recover magnets from retired electronics and wind‑turbine neodymium cores, as well as forging partnerships with Australian rare earth miners to secure upstream raw materials.
Strategic Responses and Future Outlook
The sudden swing from shortage to surplus highlights the fragility of a supply chain dominated by a single country. To reduce vulnerability, U.S. automakers and renewable‑energy developers are adopting “two‑tier” motor strategies—specifying high‑power neodymium magnets for flagship models while deploying lower‑cost ferrite magnets in entry‑level applications. Some have negotiated multi‑year contracts with Chinese suppliers that include volume‑commitment clauses and price‑cap provisions, hedging against future policy shifts.
On the public policy front, Washington is exploring the creation of a strategic magnet reserve, akin to oil stockpiles, to buffer against sudden export curbs. Federal agencies have initiated pilot programs to test magnet‑recovery technologies capable of reclaiming up to 90% of rare earth content from scrap. Meanwhile, energy‑sector stakeholders advocate for a standing U.S.‑China critical‑minerals working group, designed to provide early warning of export‑control changes and coordinate on environmental and safety standards for mining and processing.
Analysts caution that the quarterly licensing cycle now used by Beijing gives China the flexibility to throttle shipments again if geopolitical tensions flare. Should U.S.‑China relations deteriorate, fresh export controls on magnets or upstream rare earth oxides could be imposed with little advance notice, potentially reigniting manufacturing disruptions. This dynamic has spurred U.S. firms to accelerate investments in domestic magnet‑making facilities—several announced projects in Texas and California are slated to break ground later this year—but full-scale production at competitive cost remains years away.
In parallel, some consumers of rare earth magnets are evaluating alternative motor designs that reduce or replace critical elements. Research partnerships between national laboratories and private companies are exploring novel alloys with lower neodymium content, as well as entirely different magnetic materials—such as iron‑nitride formulations. Though promising, these technologies require extensive testing and certification before they can be adopted at scale in safety‑critical applications like electric vehicles and wind turbines.
For now, U.S. manufacturers are breathing a collective sigh of relief as the June deluge of Chinese magnets arrives at their production lines. Yet the broader lesson is clear: until the United States diversifies its supply chain and builds robust domestic capacity, its clean‑energy and advanced technology ambitions will remain at the mercy of external policy decisions. As demand for electric vehicles and renewable power continues its torrid rise, so too will the struggle to secure the magnets that drive the modern energy transition—leaving industry leaders and policymakers alike to grapple with the challenge of turning today’s temporary fix into tomorrow’s strategic resilience.
(Surce:www.wsj.com)
Licensing Reforms Unleash Backlogged Shipments
In April, Chinese authorities added key magnet grades and rare earth compounds to an expanded export‑control list, triggering a licensing bottleneck that left hundreds of shipments in limbo. Exporters faced wait times of six to eight weeks for approvals, leading to missed production targets in Detroit and delayed wind‑farm installations across Texas and the Midwest. Under pressure from Beijing’s trade negotiators and frustrated U.S. industry representatives, China’s Ministry of Commerce moved swiftly in late May to streamline procedures. By early June, hundreds of pending applications were approved overnight, clearing the backlog and allowing exporters to dispatch cargoes that had accumulated over two months.
Customs data show U.S.‑bound magnet exports jumping more than 660% from May to June, a surge driven less by fresh orders than by fulfillment of existing contracts. Many shipments arrived at West Coast and Gulf Coast ports stacked high on container ships, with brokers arranging urgent trucking to battery and motor factories. Within days, assembly lines at several electric‑vehicle gigafactories had been revived, and delayed rotor components for offshore wind farms were en route to coastal staging yards. Manufacturers report that as much as 70% of the magnets delayed in spring have now reached production floors, alleviating immediate shortages but also raising questions about the reliability of future supplies.
Industry Impacts Across the Energy and Tech Sectors
Rare earth magnets—most notably neodymium‑iron‑boron (NdFeB) varieties—are the powerhouse behind high‑efficiency electric motors, wind‑turbine generators, robotics and aerospace actuators. Their exceptional magnetic strength and resistance to demagnetization make them irreplaceable in many next‑generation technologies. With domestic U.S. refining capacity still in its infancy, American manufacturers have for years depended on Chinese‑made magnets to meet rising demand.
The June surge has mitigated short‑term supply pains, allowing automakers to resume planned production increases. Several major EV producers noted that magnet shortages had risked delaying the launch of new battery‑electric models, but June’s deliveries have enabled them to keep annual output targets intact. In the wind‑energy sector, turbine OEMs report that backlog reductions now clear the way for scheduled installations of several gigawatts of new capacity before year‑end—projects that had faced months‑long delays.
Yet the reprieve is temporary. Over 90% of the world’s rare earth magnet manufacturing capacity resides in China, and roughly 60% of refined rare earth oxides likewise originate there. While U.S. policy measures—such as $2.8 billion in CHIPS and Science Act funding and a national Critical Minerals Strategy—aim to jump‑start domestic mining and separation plants, experts estimate that commercial output won’t reach meaningful scale until at least 2027. In the interim, American firms are pledging billions to build recycling programs that recover magnets from retired electronics and wind‑turbine neodymium cores, as well as forging partnerships with Australian rare earth miners to secure upstream raw materials.
Strategic Responses and Future Outlook
The sudden swing from shortage to surplus highlights the fragility of a supply chain dominated by a single country. To reduce vulnerability, U.S. automakers and renewable‑energy developers are adopting “two‑tier” motor strategies—specifying high‑power neodymium magnets for flagship models while deploying lower‑cost ferrite magnets in entry‑level applications. Some have negotiated multi‑year contracts with Chinese suppliers that include volume‑commitment clauses and price‑cap provisions, hedging against future policy shifts.
On the public policy front, Washington is exploring the creation of a strategic magnet reserve, akin to oil stockpiles, to buffer against sudden export curbs. Federal agencies have initiated pilot programs to test magnet‑recovery technologies capable of reclaiming up to 90% of rare earth content from scrap. Meanwhile, energy‑sector stakeholders advocate for a standing U.S.‑China critical‑minerals working group, designed to provide early warning of export‑control changes and coordinate on environmental and safety standards for mining and processing.
Analysts caution that the quarterly licensing cycle now used by Beijing gives China the flexibility to throttle shipments again if geopolitical tensions flare. Should U.S.‑China relations deteriorate, fresh export controls on magnets or upstream rare earth oxides could be imposed with little advance notice, potentially reigniting manufacturing disruptions. This dynamic has spurred U.S. firms to accelerate investments in domestic magnet‑making facilities—several announced projects in Texas and California are slated to break ground later this year—but full-scale production at competitive cost remains years away.
In parallel, some consumers of rare earth magnets are evaluating alternative motor designs that reduce or replace critical elements. Research partnerships between national laboratories and private companies are exploring novel alloys with lower neodymium content, as well as entirely different magnetic materials—such as iron‑nitride formulations. Though promising, these technologies require extensive testing and certification before they can be adopted at scale in safety‑critical applications like electric vehicles and wind turbines.
For now, U.S. manufacturers are breathing a collective sigh of relief as the June deluge of Chinese magnets arrives at their production lines. Yet the broader lesson is clear: until the United States diversifies its supply chain and builds robust domestic capacity, its clean‑energy and advanced technology ambitions will remain at the mercy of external policy decisions. As demand for electric vehicles and renewable power continues its torrid rise, so too will the struggle to secure the magnets that drive the modern energy transition—leaving industry leaders and policymakers alike to grapple with the challenge of turning today’s temporary fix into tomorrow’s strategic resilience.
(Surce:www.wsj.com)